Predictive maintenance has emerged as an innovative approach to industrial asset management, set to play a central role in the future of the global industry.
Predictive maintenance is an industrial maintenance approach that utilizes advanced technologies such as sensors, data analysis, and artificial intelligence algorithms to predict when a machine or equipment may fail or require maintenance before serious problems occur.
This approach is based on the continuous collection of real-time data during equipment operation.
The central idea of predictive maintenance is to identify patterns and trends in machine operation data, enabling operators and maintenance technicians to take corrective actions at the right time.
This contrasts with traditional corrective maintenance, where interventions only occur after a failure or breakdown, resulting in unplanned and potentially costly downtime.
In this article, we will explore the reasons why this methodology is rapidly emerging as an inevitable choice for companies seeking efficiency and cost savings.
Sustained Cost Reduction
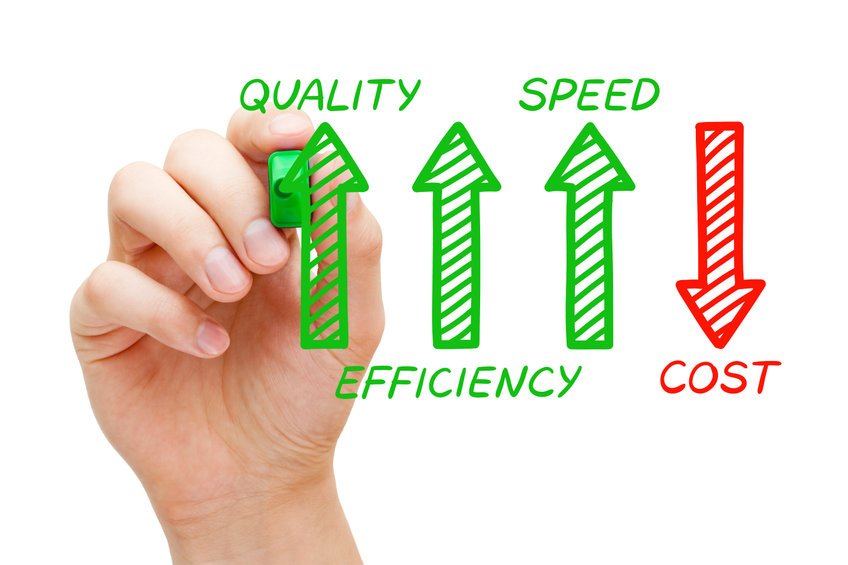
Predictive maintenance offers an invaluable competitive advantage by significantly reducing maintenance costs.
With the ability to anticipate failures and issues before they occur, companies can effectively plan maintenance, avoiding costly emergency repairs and minimizing unplanned downtime.
As a result, significant savings in operational costs are achieved.
Enhanced Reliability
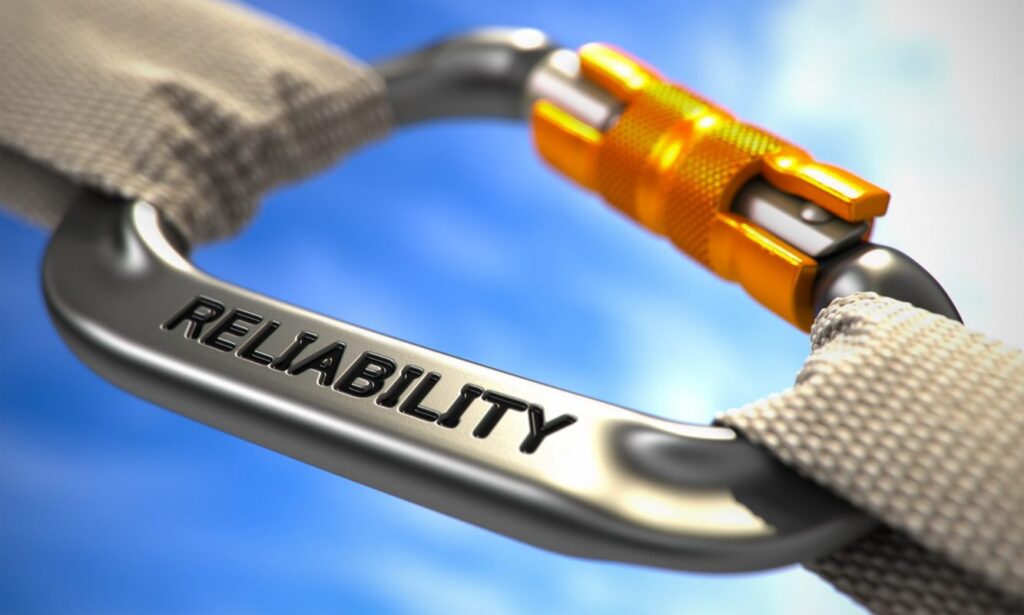
Predictive maintenance raises the bar for the reliability of industrial assets.
By continuously monitoring machine operating conditions, issues are identified at early stages, enabling proactive correction before they worsen and cause irreparable damage.
Consequently, the reliability and lifespan of equipment are significantly extended.
Maximizing Asset Availability
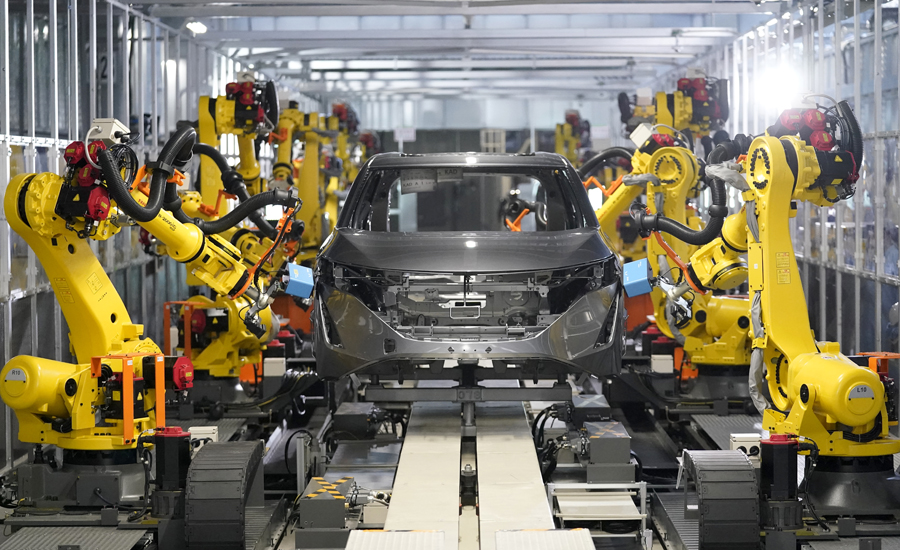
One pillar of predictive maintenance is maximizing asset availability.
With the ability to predict when maintenance will be needed, companies can schedule production interruptions during periods of lower demand or at more convenient times.
This results in fewer unplanned interruptions and greater asset availability to meet production needs.
Intelligent Maintenance Optimization
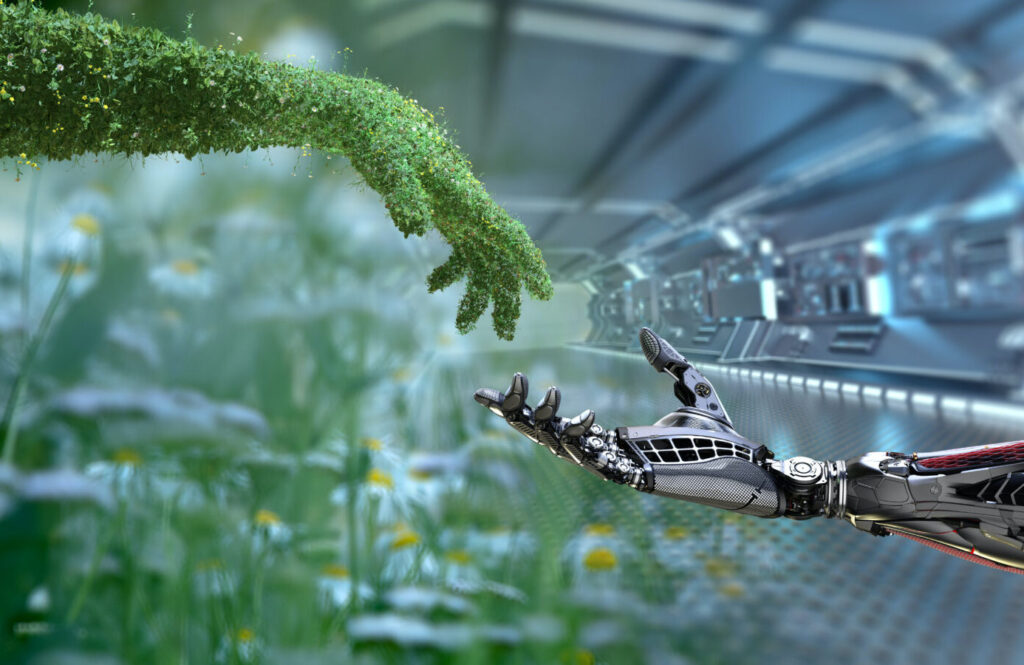
Advanced data analysis plays a crucial role in predictive maintenance.
Machine learning algorithms can identify complex patterns in operation and maintenance data, enabling continuous optimization of maintenance processes.
This leads to more efficient resource utilization, cost reduction, and improved operational performance.
Prioritizing Safety
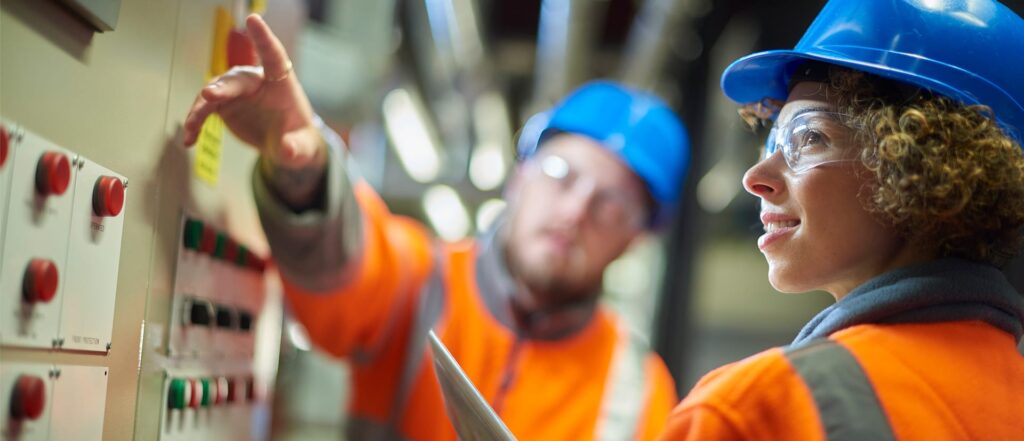
Predictive maintenance also significantly contributes to worker and industrial safety.
By detecting problems before they become critical, it helps prevent hazardous situations such as leaks of hazardous substances or catastrophic failures.
This not only protects employees but also prevents environmental damage and potential litigation.
Prediction and Sustainability
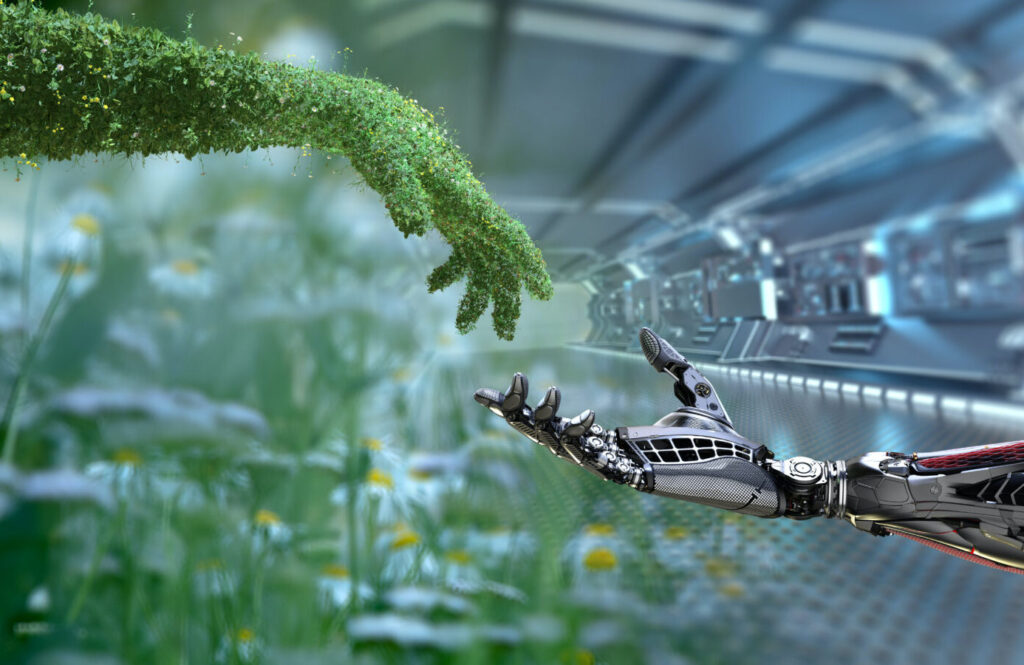
Predictive maintenance is aligned with sustainability principles.
By avoiding premature asset replacement and minimizing resource waste, it contributes to reducing the environmental impact of the industry.
Furthermore, maintenance optimization leads to more efficient energy and material usage, promoting more sustainable practices.
Predictive maintenance is unquestionably the future of the industry.
Its ability to reduce costs, enhance reliability, improve asset availability, optimize maintenance, ensure safety, and promote sustainability make it an indispensable strategy for companies aiming to remain competitive in an ever-evolving industrial landscape.
As technologies continue to advance, and organizations adopt smarter approaches to asset management, predictive maintenance will continue to play a central and undeniable role in the future of the industry.
If your organization is already embracing predictive maintenance or embarking on this journey with solutions like IBM MAS8, MaxMatters is prepared to assist your company in optimizing its technology investments for maximum performance.
Visit our contact page and schedule a meeting with one of our consultants »
We look forward to assessing how our technological solutions can elevate your organization’s performance.